The Scissor Lift Hire Guide
Scissor lifts are indispensable equipment in the construction industry, offering versatility and efficiency in accessing elevated work areas. However, ensuring their safe and effective use requires careful consideration both before, and during the hire period.
Therefore, we have put together a comprehensive guide for hiring scissor lifts, emphasising the key factors to consider before and during the hire process to enhance safety and productivity.
pre-hire considerations
Before selecting a scissor lift for hire, consider the following factors to ensure compatibility with your project requirements.
- Project Needs: Determine the level of work you are undertaking and if it requires a scissor lift to be performed efficiently and safely.
- Review Regulations: Familiarise yourself with any UK regulations and industry standards governing scissor lift operation and safety. The Health and Safety Executive and Government Legislation has comprehensive guidance on all working at height regulations.
- Select a Reputable Supplier: Choose a trusted tool and access equipment hire company with a record of reliability, quality of equipment, and excellent customer service.
site assessment:
You should conduct a thorough assessment of the worksite before hiring and deploying a scissor lift. When conducting a site assessment, it is important to check for the following:
- Ground Conditions: Check for stability, including slopes, uneven surfaces, and obstacles that may affect scissor lift operation
- Potential Hazards: Look out for power lines, beams, or other overhead obstacles that could pose risks to personnel or equipment
- Adequate Space: Verify that the worksite provides sufficient clearance and maneuverability for safe scissor lift operation
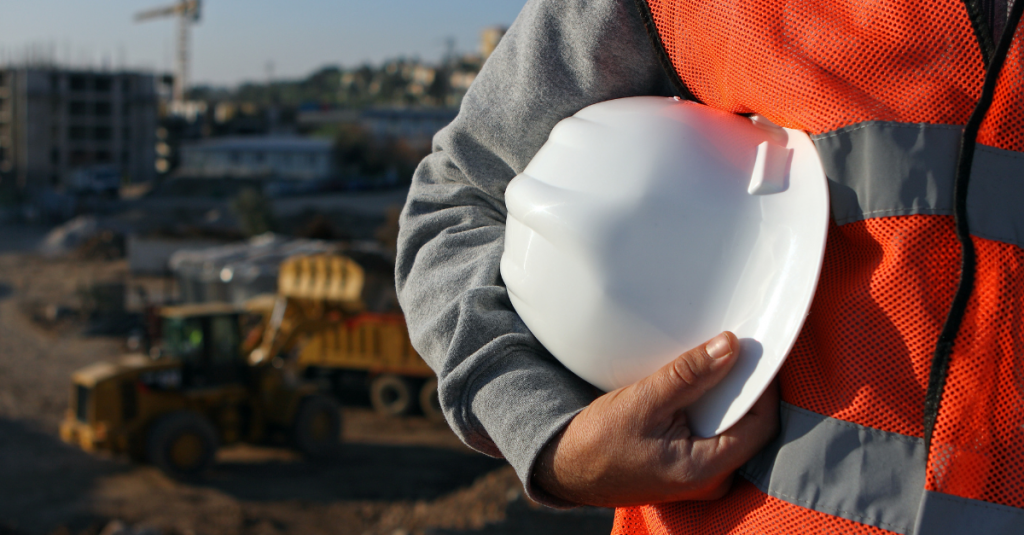
CHOOSING THE RIGHT SCISSOR LIFT:
Assessing your site will help aid in choosing the right scissor lift for your project’s specific requirements. For example, this will:
- Help to determine the required platform height, weight capacity and platform size
- Decide whether you need an indoor or outdoor scissor lift, or one that can do both
- help decide the maneuverability requirements, including the base unit size and site access
- The power requirements – Electric or Diesel?
This will help you make an informed decision on the specific requirements you need from your scissor lift and help the hire company match your specific needs.
safe use of the scissor lift during the hire:
During the hire, you will need to prioritise safety for all workers operating on and around the hired scissor lift, making sure all personnel have received adequate training. This can include:
- Operator Training: Ensure you operators are trained and competent in scissor lift operation, are familiar with safety protocols, and equipped with proper PPE. Scissor lifts come with in-built safety features, but ensuring proper PPE is used, such as safety harnesses, are crucial in reducing the risk of falls.
- Follow the Manufacturers Manual: Ensure your team have a copy of the manufacturers operating guide and adhere to it at all times.
- Risk Assessments: You should always conduct a pre-task risk assessment to identify and mitigate potential risks and hazards specific to your work environment.
It is important to remember that a scissor lift should never be used for any task that it was not intended to perform. Attempting to re-purpose or use a scissor lift for tasks beyond its intended purpose, as specified by the manufacturer, poses a significant risk of serious injury or accidents. Therefore, it is important to verify the proper usage instructions for the scissor lift and strictly adhere to them. This includes terrain, weight capacities, number of operators, and power source.
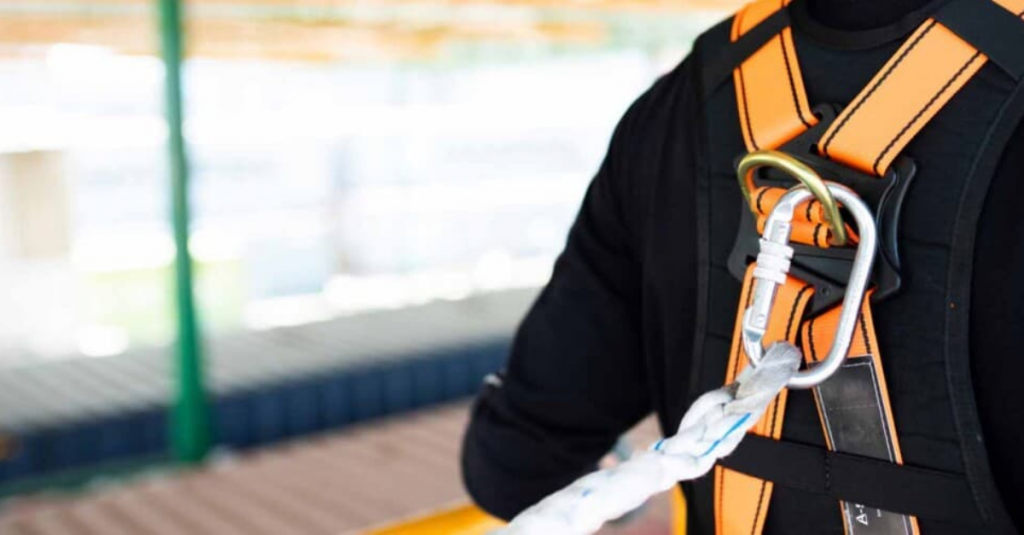
inspections and maintenance:
Although your scissor lift will have been inspected by you hire company before you receive it, its important to do a thorough inspection to confirm it is fit for purpose. Do not use the machine if there are any signs of fault or damage. Scissor lifts are designed to support workers and materials, and any damage or faults will stop it from functioning properly. Significantly increasing the risk of accidents and injury. Here are some things to check:
- Control systems
- Hydraulic systems
- Brakes
- Safety features (including emergency controls)
- Tyres
It is important to immediately address any identified issues or safety concerns to prevent accidents. These should be identified to your supplier who can schedule in an engineer or sort you a replacement.
Read our 6 Best Practice Tips for Powered Access On-site
preparing for an emergency:
You should always be prepared for emergencies and establish procedures and protocols should you need them. These should be communicated to your team, and can include:
- Emergency Training: Train your operators on emergency procedures, including how to safely lower the scissor lift in case of power failure or malfunction.
- Access to Emergency Equipment: Ensure access to emergency contact information, rescue equipment, and first aid supplies.
- Regular Review and Practice: Regularly review and practice emergency procedures with personnel to promote readiness and effectiveness.
conclusion:
There is a lot to think about when hiring a scissor lift for your project but ensuring you have considered all aspects of its operational uses, safety protocols, and hire requirements is important for the smooth and safe flow of your projects.
By being informed, you’re not only reducing the risk of accidents or injuries but also safeguarding against the associated costs and disruptions. Investing in safety is not just a responsibility; it is an investment in the health of your workforce and business.
Be sure to check out the full range of MEWPS available on our extensive hire fleet
further reading:
A BRIEF GUIDE TO ACCESS SOLUTIONS ON UK CONSTRUCTION SITES
FEATURED PRODUCT: THE GENIE ELECTRIC SCISSOR LIFT
Please Note: The recommendations in this article are for general information only. Always refer to your organisation’s specific guidelines and procedures when implementing any techniques, practices or procedures.