HOW ON TIME DELIVERIES HELP REDUCE DELAYS ON SITE
WHAT IMPACT CAN DELAYS HAVE ON YOUR BOTTOM LINE?
We look at how on time deliveries can help reduce delays and minimise blockers on site – directly impacting your bottom line.
We know delays to construction projects are often considered inevitable – part and parcel of the industry so to speak. There is a general acceptance that it is highly unlikely that any project will run without some sort of delay or blocker along the way.
OVER 85% OF RESPONDENTS SAID THEY HAD EXPERIENCED DELAYS ON RECENT CONSTRUCTION PROJECTS.
Indeed, delays have become such an accepted occurrence on-site, that according to construction performance research conducted by Cornerstone Projects most contractors anticipated that up to 30% of their projects would be subject to delays.
Over 85% of respondents from the same survey said they had experienced delays on recent construction projects.
WHAT ARE THE COMMON REASONS FOR ON SITE DELAYS?
There are all sorts of reasons for delays – some easier to control than others. For example, extreme weather conditions are out of our control and no amount of planning will prevent them having some sort of impact.
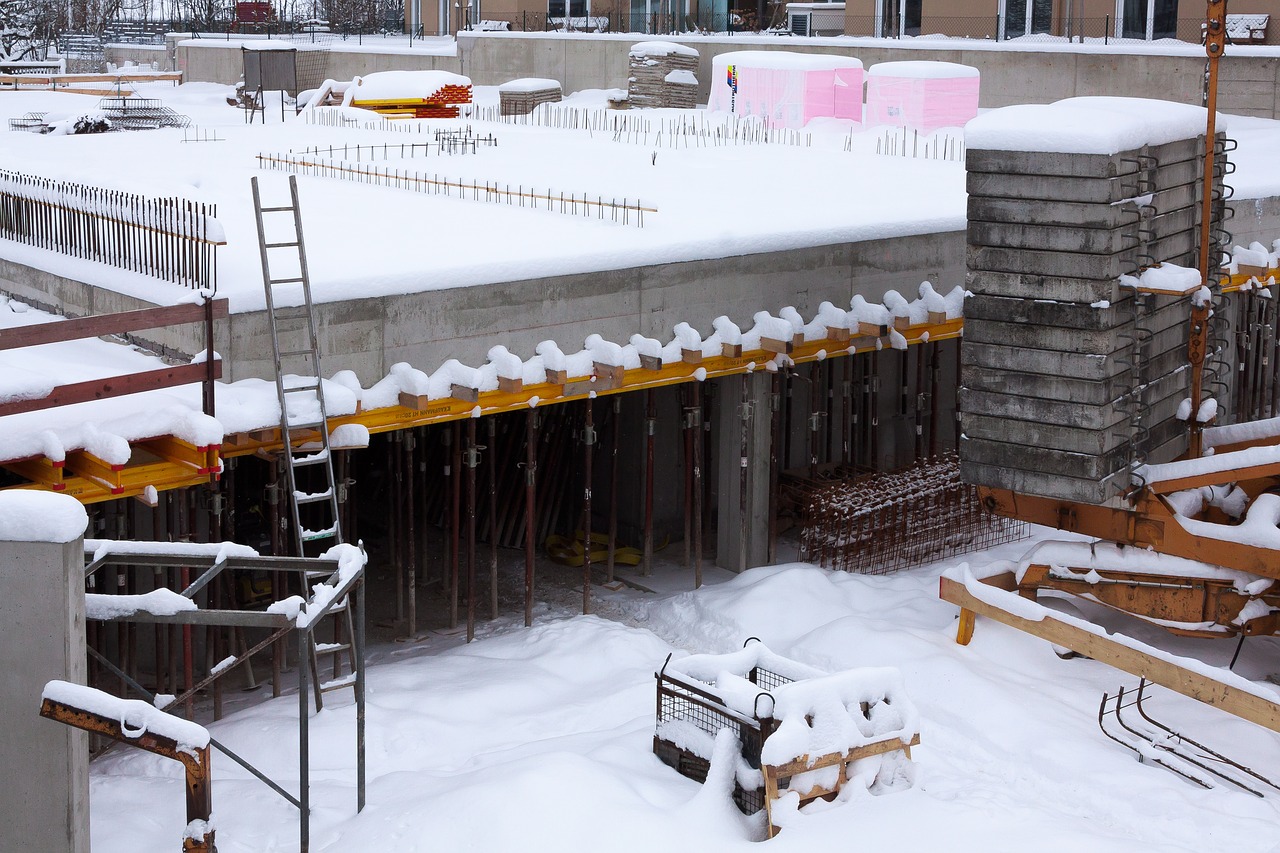
And, of course, we have just experienced first-hand the setbacks Covid-19 caused across the entire construction industry.
However, many of the reasons cited for causing delays on site are things that could be prevented with planning.
- Poor communication between multiple parties – contractors, sub-contractors and suppliers.
- Budget – misquotes and underestimating costs
- Poor scheduling – delays in the delivery of equipment, materials, and goods to site.
- Delays in the collection of tools and equipment off site.
WHAT IMPACT CAN DELAYS HAVE ON YOUR BOTTOM LINE?
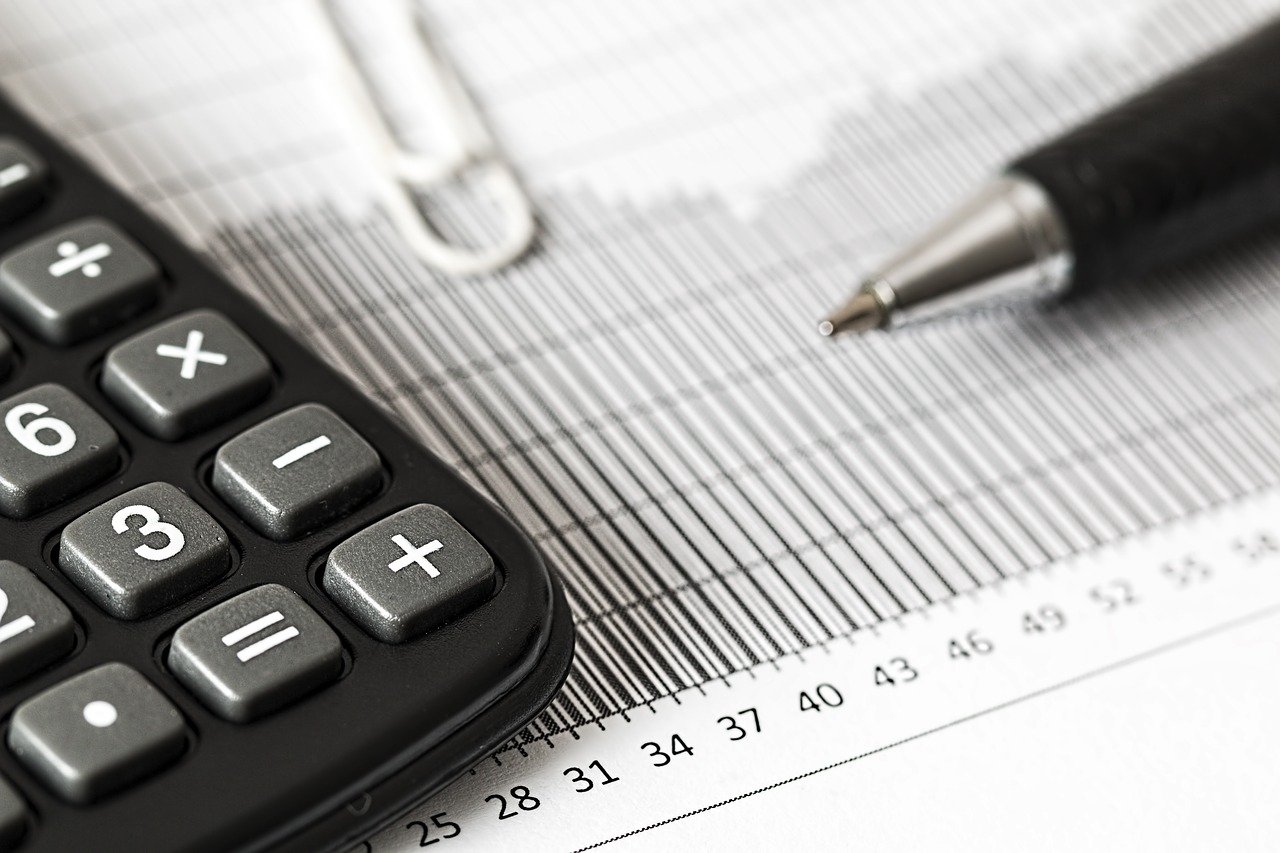
Especially in the current economic environment, with the tightening of belts and reduced budgets, the construction industry is under increasing pressure to reduce the turnaround time on projects.
Delays don’t just mean wasted time on site alone, delays and blockers have a direct impact on the bottom line. According to a recent report:
- Fewer than 1-3 contractors (30%) finish their project on time within budget
- Delays are costing companies up to 20% more than the estimated costs.
Cost implications can come in terms of additional labour costs, penalty clause penalisation for going over agreed deadlines, and wasted hours on site.
On time deliveries matter
Delays in the delivery of equipment, tools, and materials can amount to a significant dent in the bottom line
According to Glenn Hawkins, Head of BSRIA’s Process and Productivity Department:
“about 8-9% of the working day is lost by a typical tradesman waiting for or collecting materials, tools and equipment.”
This amount of wasted time becomes even more sobering if you extrapolate those hours. If you base this finding on a typical working day of 8 hours, it equates to a staggering 195 hours wasted over a year – and that is based on just one worker alone.
These delays are not only frustrating due to the significant time lost every year caused by waiting around for deliveries and collections. You can have skilled trades (at high expense) on-site ready to begin work but stuck twiddling their thumbs waiting for tools and equipment to turn up. This is not only wasted time but a sizeable cost implication.
Because construction projects are often sequential, it may also have the knock-on effect of becoming a blocker to other jobs you have scheduled in.
For example, you may have hired in tools and equipment for a specific task that needs to be completed before another can start. If the delivery is delayed, then it becomes a blocker – impacting all the subsequent jobs that need to follow on from its completion.
HOW TO MINIMISE THE IMPACT OF CONSTRUCTION DELAYS
Whilst some delays are out of even the best project manager’s control, good forward planning and communications can help either manage or entirely prevent many others.
By ensuring that preventable delays don’t occur, you can reserve your energy for fire-fighting those that even great planning can’t control.
Many delays are not inevitable and implementing positive practices such as:
- Thorough preparation and project planning
- Realistic, advance scheduling
- Transparent and collaborative communications
- Crisis planning
All these will help towards minimising the number of delays and blockers.
ON time deliveries – THX CAN HELP YOU REDUCE EQUIPMENT AND TOOL DELAYS
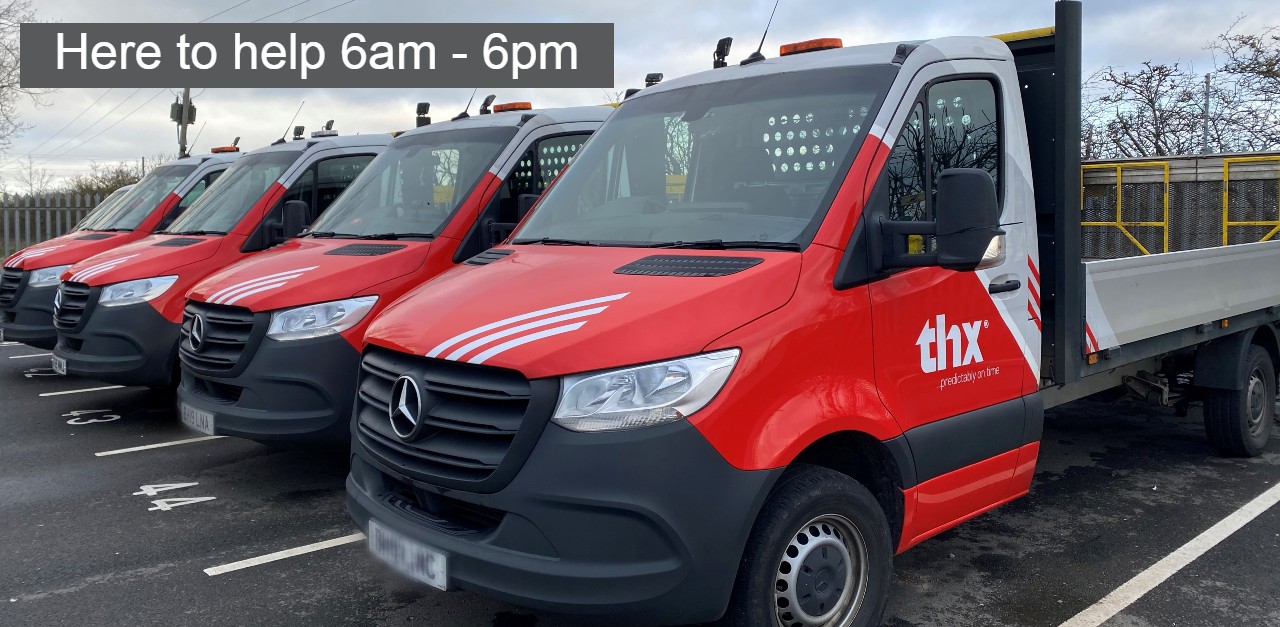
Established in 2006, THX has many years’ experience within the hire industry. We understand the problems that can escalate when much-needed equipment and tools fail to materialise when required and expected.
At THX we know that quick turnaround, on time deliveries, on time collections and good communications are all key factors in reducing delays related to hire.
Next day deliveries and two-hour time slots
With increased pressure on turnaround times, hiring tools and equipment is a quick and efficient way to get tools on (and off) sites as and when you need them.
We provide next day deliveries and customers can choose two-hour time slots (on both deliveries and collections).
On-time deliveries – over 98% of our deliveries are on time1
We never underestimate the importance to our customers of delivering on time. So much so, you can be confident that we will deliver when we promise. And, if we fail, you receive a week’s free hire.
Reliable off-hire collections – off-hires collected within an average of 1.3 days2
We also recognise that many hire companies underplay the importance of collections – often playing second fiddle to deliveries.
In addition to time wasted waiting for late collections, we know that equipment left hanging around will impact on the handover of a completed project. And, increase the likelihood of cost incurred through theft.
The average number of collection days for tools and equipment in the hire industry is currently estimated to be about 5.1 days. At THX we target a collection turnaround of 1.5 days – averaging just 1.3days between Jan – Dec 2020
First class relationships – live tracking and transparent communications
Poor communication is another consistent problem with the hire industry. It can lead to missed deliveries and on-site delays.
Here at THX, we pride ourselves on building strong, long-term relationships with our customers. Not only do our account holders have a key account manager, our expert team of customer service operatives are ready to help from 6am, Monday to Friday. What’s more, because they are all onsite at our Superhub depot , there is no being passed from pillar to post across different branches.
Whilst some on site delays will always remain out of our control, delays and blockers caused through late deliveries and collections are preventable with some consideration and planning.
At THX we believe that delays caused by late deliveries and collections are preventable, which is why we offer two-hour timed delivery slots, quick collections and seamless and transparent communications across your entire hire experience.
Let THX help – Open and Account Today
1 Jan – Dec 2020 – averaged over 98% of on-time, in full deliveries
2 Jan – Dec 2020 – average 1.3 collection days