National Back care awareness Week – Top Tips for safe manual handling.
The Manual Handling Operations Regulations (MHOR) define manual handling as “ … any transporting or supporting of a load (including the lifting, putting down, pushing, pulling, carrying or moving thereof) by hand or bodily force.”
Manual handling is a common activity in almost every workplace. However, performing any of the above listed tasks without a proper risk assessment or sufficient training can significantly affect workers’ health. We’ve put together this guide on the factors you need to consider before any manual handling takes place.
contents
The risks of manual handling
What’s the law?
Carrying out a risk assessment
How to reduce the risks
Good manual handling technique
Using lifting equipment
What to do in the event of an injury
THE RISKS OF MANUAL HANDLING
According to SHP, almost a fifth of the 51,211 non-fatal injuries reported by employers were due to handling, lifting or carrying. This staggering statistic means that employers and workers must all be vigilant of the risks and take steps in order to reduce the likelihood of injuries in the workplace.
Inappropriate manual handling often leads to musculoskeletal disorders (MSDs) such as pain and injury to the arms, legs, and joints, as well as repetitive strain injuries. With 473,000 workers reportedly suffering from work-related MSDs in 2022/2023 (HSE, 2023)
HSE also state that up to 3.7 million working days are lost every year due to non-fatal workplace injuries, a large portion of which are a result of poor manual handling techniques. These can occur anywhere in the workplace, and various factors can increase the risk, including awkward posture and previous or existing injuries.
Many lifting and handling injuries are cumulative, so even if an injury is not immediately present, handling objects in an incorrect way can have serious implications in the future, both for the employee and employer. Because of this, manual handling should always play a central role in occupational safety.
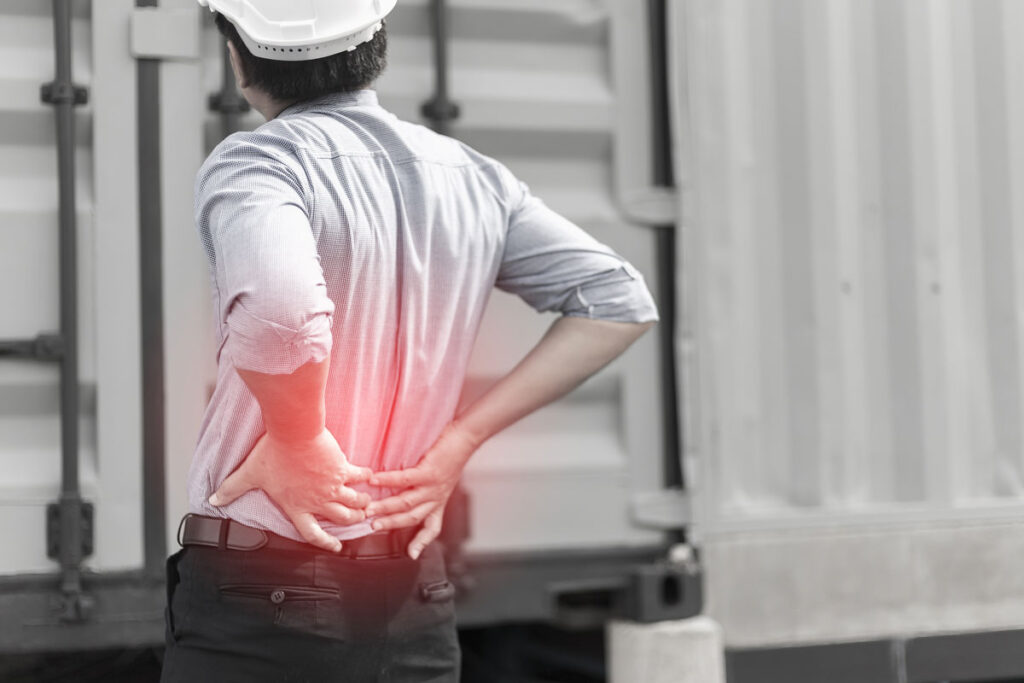
WHAT’S THE LAW?
All employers must comply with the Manual Handling Operations Regulations (MHOR) introduced in 1992, which was developed to reduce the number of MSDs at work due to the escalating statistics. These regulations cover how to avoid, assess, reduce the risk of injury from manual handling and include a ‘hierarchy of measures’ to follow.
To deal with the risks that arise from manual handling, the MHOR says that you should:
- First: avoid hazardous manual handling operations so far as is reasonably practicable
- Second: assess any hazardous manual handling operations that cannot be avoided
- Third: reduce the risk of injury so far as is reasonably practicable
The law doesn’t specify a maximum weight limit to be lifted by employees but places the responsibility with the employer to manage the risks and take safety precautions that will depend on the specific manual handling task.
Risk assessments must be carried out and must take into account the individual’s strength and health, the weight of the load, and the distance it needs to be carried. The nature of the load and the posture that would need to be adopted must also be considered, as well as the possibility of using equipment to help.
The MHOR do give basic guideline figures for lifting and lowering, but it’s important to remember that these alone will not eliminate the risk of injury. Every situation and load is different, and so should be approached with a new perspective. The general guidelines for lifting and lowering are outlined in Figure 1 of HSE’s Manual handling at work guide.
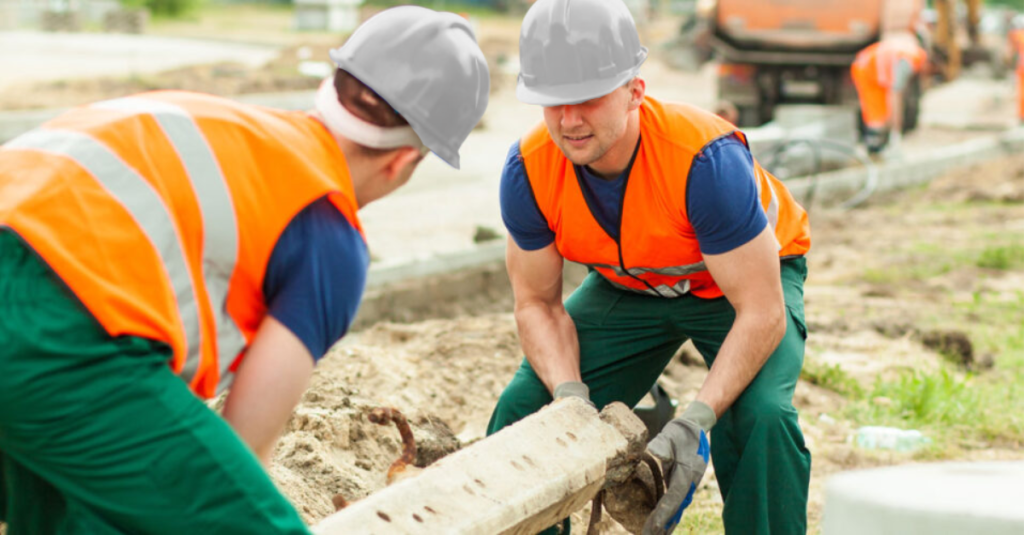
CARRYING OUT A RISK ASSESSMENT
As previously mentioned, a risk assessment should always be carried out before a lift is attempted. There are several factors to be considered, which can be summarised into Task, Individual, Load, Environment and Other Factors (TILEO). Here are some of the crucial questions that need to be asked:
TILEO
TASK – Does it involve twisting, stooping, bending, excessive travel, pushing, pulling, precise positioning of the load, sudden movement, inadequate rest or recovery periods, team handling or seated work?
INDIVIDUAL – Are they pregnant, disabled, suffering from health problems?
LOAD – Is it heavy, difficult to grip, sharp, hot, cold or have contents that are likely to move?
ENVIRONMENT – Are there space constraints or flooring that is uneven, slippery, unstable? Are there differences in floor levels? Is the climate hot, cold, humid?
OTHER FACTORS – Could movement or posture be affected by the clothing or PPE being worn? Are they wearing the correct PPE?
In some cases, a risk assessment will deem the task unsafe and, in these situations, you must assess whether bringing in help, such as other employees or lifting equipment, will reduce the risk to an appropriate level for the lift to go ahead. It is always better to be over-prepared before a lift than to risk injury. Safety organisations such as RoSPA offer courses on manual handling risk assessments to increase your awareness and knowledge of all the correct procedures.
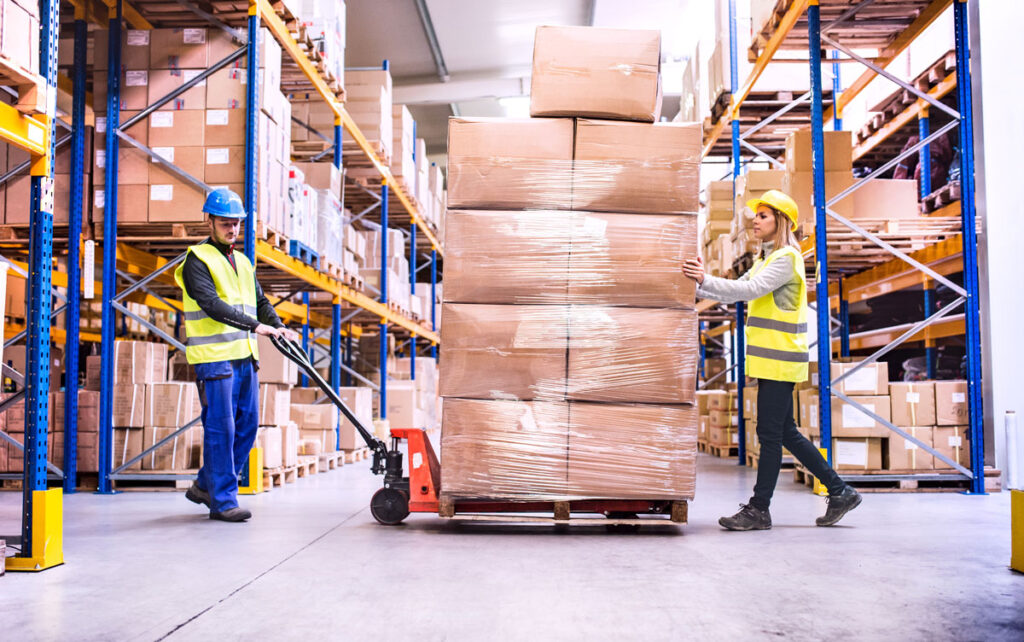
HOW TO REDUCE THE RISKS
Where possible, it is best to avoid lifting and handling manually by using automation or assistance. If lifting equipment is to be used, you must make sure that it is in working order and that employees have been fully trained on how to operate it correctly. Even if the load still needs to be manually lifted for part of the journey, lifting aids can be used to reduce the carrying distance, therefore, reducing the risk of an accident.
In some cases, it may just be that more than one worker is required to lift the load if the weight is too much for one person. Encourage employees to ask their colleagues for assistance when it is needed. If the load can be broken down into smaller parts then this may help to reduce the weight enough for one person to safely lift.
The lift should always be planned before it is attempted. This includes ensuring that the path to the destination is decided and is clear of potential obstacles, including other workers.
Consider the height at which the items to be lifted are stored. Lifting below knee height or above shoulder height puts increased strain on the spine, so where possible the storage place should be reached without causing the employee to adopt an awkward posture.
All employees should be trained to follow good manual handling techniques. Unfortunately, there is no ‘correct’ way as every item and environment is different, but there are recommended techniques that address the general risks associated with manual handling. They should also be supplied with suitable PPE such as steel toe capped boots and gloves.
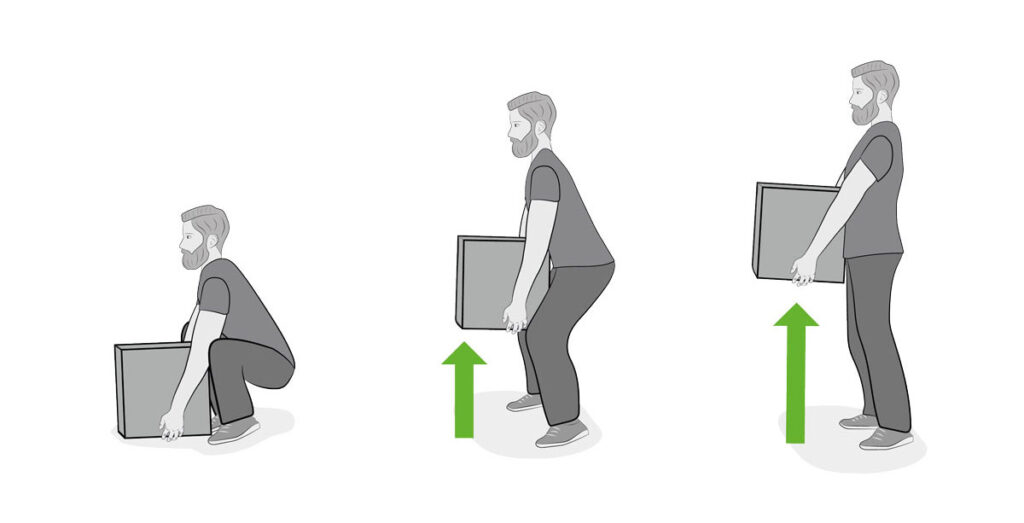
GOOD MANUAL HANDLING TECHNIQUE
Whilst there is not a manual handling technique that can be applied to every single task, the HSE provide general guidance for good practice:
Once you have planned the lift and all obstructions have been cleared the employee will have to get into the right position, with their feet apart and one leg slightly forward to maintain balance.
The load should be hugged as close to the body as possible so that the body can be used for stability rather than only relying on the hands. Ensure that the heaviest side is next to the body and close to the waist if possible. If this close approach is not possible, then it may need to be slid towards the body before the lift is attempted.
Then it’s time to start the lift. As the employee begins, they should slightly bend their back, hips, and knees and avoid stooping or squatting. It is also better to avoid twisting or leaning sideways, but instead, keep the shoulders level and facing the same direction as the hips. Turning can be done using the feet rather than the back.
Looking ahead is also important, rather than looking down at the load. Once the employee has a secure hold on it, they should focus on the route ahead, in case they encounter any obstacles. Movement should be smooth to reduce the likelihood of the goods jerking or snatching on anything, which could increase the risk of injury.
If the load needs to be placed precisely in a particular position, in storage, for example, it should be placed down first and then slid into position.
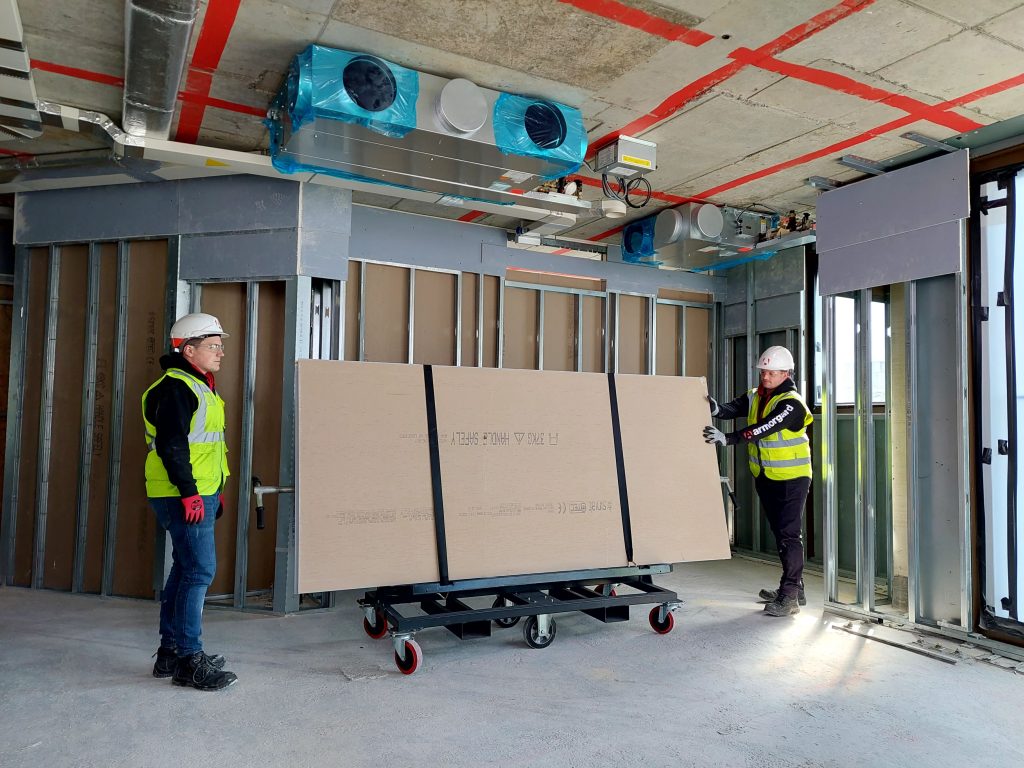
USING LIFTING EQUIPMENT
No one should lift or handle more than they can easily manage, so if an item is too heavy than alternative lifting methods must be considered. There are several different types of equipment that will be useful for reducing the need for manual handling on site. These include hoists, conveyors or even forklift trucks.
You can avoid manually manoeuvring heavy items on site by using a turntable truck, or using a material lift for when there is restricted space. If you need to transport pavers and blocks straight from the pallet you can opt for a block cart.
Going up the stairs while manual handling can be a serious hazard as there is a lack of visibility. This can be avoided with a powered stair climber, which makes the stairs easy to climb and takes the weight of the full load away from the worker.
Lifting large and awkward materials such as plywood and plasterboard, can be hard and wearing on employees backs. Using aids such as the Armorgard Adaptakart can both increase job efficiency, and safety at the same time. Every workplace will have different requirements for lifting equipment. If you would like more information on hiring handling and lifting equipment get in touch with the THX team today.
WHAT TO DO IN THE EVENT OF AN INJURYWorkers must stop immediately and safely place the load down or stop pushing/pulling if they are experiencing any pain. Every incident should be recorded in an accident book no matter how minor it appears to be at the time, as in some cases the full damage can become present hours later. Consider how the accident could have been avoided and, if appropriate, re-evaluate the safety procedures, equipment or lifting technique for that task to avoid the same issue arising again.
For more guidance on handling and lifting equipment, feel free to get in touch with our team today to discuss the best options for your workplace. Call us on 01234 871320 or email hire@thxuk.com
Please Note: The techniques and best practices outlined in this article are for general information only. Always consult your organisation’s health and safety guidelines and procedures. For specific advice related to your work environment, please refer to your health and safety representative.